Throughout the development of TPMS products in recent years at home and abroad, it can be seen that the development of foreign TPMS products mainly focuses on the research of smart sensors, and the TPMS transmitting modules will be developed in the direction of high integration, singularity and passive. This paper describes the design principles of a new TPMS transmission and acceptance. In the design, Motorola's integrated chip MPXY8020A for TPMS is used as the main component of the tire pressure detecting unit, which further reduces the system volume and reduces the power consumption of the system. The system not only displays the collected pressure and temperature values, but also The values ​​are sent to the bus in CAN format, and the subsystems attached to the CAN bus make measures based on the received messages, which makes the importance of the tires more and more obvious. If the engine module is attached to the CAN system, if the data collected from the bus indicates that the pressure value is lower than the standard value, it can be decelerated to avoid wear and tear on the engine system [2]. And add a pressure relief module on the popular TPMS module, so that the tire pressure can never reach the overpressure to the puncture state, making our driving more safe and reliable. Tire intelligent pressure monitoring system works
1.1 Tire intelligent pressure monitoring system The principle of pressure measurement It uses lithium sub-battery as the power source. It directly measures the air pressure and temperature of the tire through the pressure temperature sensor implanted in the tire, and transmits it through wireless modulation. The central monitor module receives it wirelessly. The received tire pressure, temperature signal and module status are processed, and the tire pressure and temperature can be displayed in turn through the display part. The driver can intuitively understand the temperature and temperature of each tire, and take relevant measures according to the prompt; when the tire pressure is too high, If the temperature is too high, the system will automatically alarm when the temperature is too high.
1.2 Tire intelligent pressure monitoring system Pressure relief principle Install a safety valve on the valve. The safety valve is used to prevent the pressure in the system from exceeding the allowable pressure to protect the puncture due to excessive pressure to ensure safe driving.
Figure 1 shows the working principle of the safety valve. The input port of the valve is connected to the control system (or device). When the system pressure is less than the set pressure of the valve, the spring force presses the valve core against the valve seat, as shown in Fig. 1(a). When the system pressure is greater than the set pressure of the valve, the spool is opened and compressed air is discharged from the R port to the atmosphere, as shown in Figure 1(b). Thereafter, when the pressure in the system drops to the valve setting, the valve closes and remains sealed.
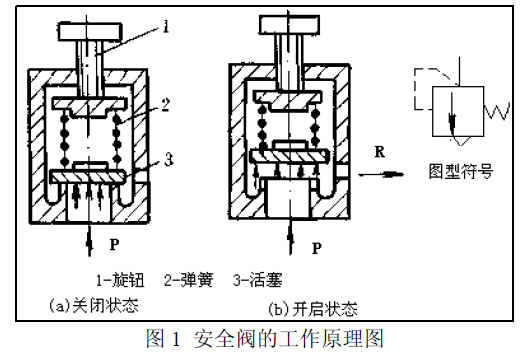
Hardware design of tire intelligent pressure monitoring system The whole system consists of three parts: tire inner module, pressure relief module and central controller. Figure 1 is a structural diagram of the tire pressure monitoring system, including high-precision integrated sensor MPXY8020 [3], intra-tire micro-control and transmitter MC68HC908RF2 [4], RF receiver MC33594, main microcontroller MC68HC908GZ16, CAN bus driver TJA1050T.
This article refers to the address: http://
2.1 In-tire module Figure 3 shows the schematic diagram of the tire module circuit. The module is mounted on the tire valve core and is powered by a lithium battery. The crystal frequency of the RF chip is 9.84 MHz. The FSK emission modulation mode is selected by setting the MODE pin low, and the transmission frequency is 434 MHz [5]. Loop antenna technology is used in the design of antenna printed circuit [6].
2.2 Central module The central module includes RF receiving and processing module, alarm display module and CAN bus transceiver module. The function of the RF and central processing module is that the RF receiver chip MC33594 demodulates the signal and sends it to the MC68HC908GZ16 for data processing. It displays through the digital tube, performs sound and light alarm through the buzzer LED, and notifies other CAN subsystems. Effectively prevent punctures and reduce wear and tear on other systems. The hardware circuit is shown in Figure 4 and Figure 5.
5 CAN transceiver module
2.3 Pressure Relief Module Install a pressure relief valve on the valve of the tire. According to the different requirements of various tires and various types of vehicles, set the maximum value that can be achieved in a tire tire. When the tire pressure exceeds this pressure value. When the pressure relief valve is automatically opened to relieve pressure, the traffic accident caused by the puncture generated under high pressure is completely avoided.
3 system software design
3.1 Tire monitoring module software design Monitoring module to complete the main functions are: initialization of each chip, pressure, temperature and limit alarm threshold comparison, when the temperature or pressure exceeds the limit of the threshold value, the pressure, temperature is accurately sampled Generate data frames and transmit data frames. The flow chart is shown in Figure 6.
3.2 Central Control Module Software Design The main control program is the main function, which completes the system work by calling each sub-module. The main functions to be completed by the receiving and reporting module are: initializing each chip, configuring the receiver MC33594, receiving data, data verification, data processing, display data, information sharing, and sound and light alarm. The data check includes tire module ID check and data CRC check. If the received tire module ID number is the ID of the tire module in the system, the CRC check is performed, otherwise the data is returned again. If the CRC is verified, that is, Crbb=0, the data processing is performed. The data processing compares the received temperature, pressure data and various thresholds, displays the temperature value, pressure value, tire identification and tire working status, performs sound and light alarm, and sends the data to the CAN through the CAN interface integrated by the microprocessor. On the bus, the system attached to the CAN bus realizes information sharing by sending and receiving commands and data, otherwise it re-receives data. The flow chart is as shown in Figure 7.
4 Conclusions The direct tire pressure measurement system based on the integrated sensor MPXY8020A and RF transceiver module developed in this paper is an intelligent TPMS system. The system can reasonably control the tire pressure, improve driving safety, and can effectively improve the driving comfort and fuel economy of the car; and the system can also provide relevant information for other electronic devices inside the car through the CAN bus. Further improve the performance of automotive related components. In addition, the system can not only realize real-time monitoring and alarm of tire pressure and temperature, but also protect against overpressure, making the car safer and more reliable. The author of this paper is innovative: the system utilizes the reliability, real-time and flexibility of the CAN bus, making the tire intelligent monitoring and protection system safer and more reliable. It also increases the pressure relief module, making the vehicle safer and will be caused by high pressure. The accident rate of puncture fell to a low level.
references
[1] Milin, Chen Ran, Tan Wei. Design of embedded tire pressure wireless monitoring system [J]. Instrumentation users, 2006, (13): 24-25.
[2] Zhang Lanfang. Automobile tire pressure detection and monitoring system based on CAN bus [D]. Hangzhou: Zhejiang University, 2006
[3] Freescale, MPXY8020A DataSheet, 2003.
[4] Freescale, MC68HC908RF2 Data Sheet, 2003.
[5] Qin Zheng, Hu Jianguo, Liu Zhixian. Research and implementation of intelligent monitoring system for automobile tire pressure [J]. Microcomputer Information, 2008; 3-2,: 230-232.
[6] CA Balanis, "Antenna Theory, Analysis and Design", second edition, John Wiley & Sons, Inc., 1997.
Woofer Speaker,Stage Woofer Speaker,Bass Woofer Speaker,Sub Woofer Loudspeaker
Guangzhou Yuehang Audio Technology Co., Ltd , https://www.yhspeakers.com