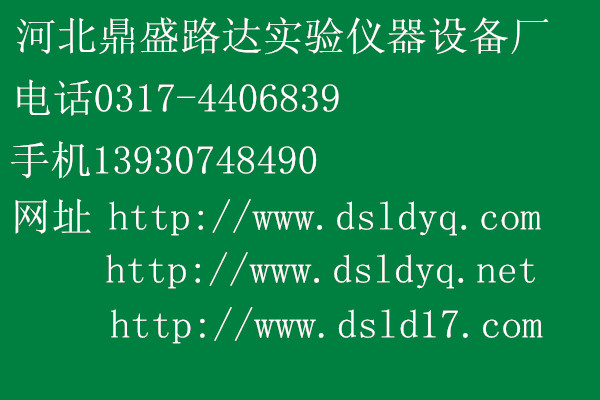
HYCX-1 automatic hydraulic rutting test forming machine is a comprehensive automatic rut test system which is introduced by the company with reference to foreign models. It has further improved the appearance structure, system index and function. It has the characteristics of high precision, fooly operation in the test process, easy to learn and easy to use and easy to maintain. The whole system consists of a host computer, an embedded control system and a PC, and test software. The main control panel of the mainframe can perform most of the operation control and is more convenient to use. The PC test software can automatically complete the test, record the test results, draw the deformation curve, automatically save the experimental data, and print the test report.
[Technical Specifications] Electrical Parameters:
Power input: host: three-phase four-wire 380V ± 10%
Controller: single phase 220V ± 10%
Heater power: △ connection method, 1KW × 3
Motor power: three-phase three-wire 750W
Total power: no more than 4.2KW
Technical indicators:
Temperature measurement range: 0-100 ° C
Temperature resolution: 0.01 ° C
Temperature measurement accuracy: initial accuracy ±0.5 °C (±0.05 °C after fixed point correction)
Temperature control accuracy (relative to temperature measurement point):
Cabinet temperature: ±0.2°C after 45 minutes and ±0.05°C after 60 minutes
Sink temperature: ±0.5°C after 30 minutes and ±0.2°C after 45 minutes
Temperature difference between different positions of the cabinet: after 60 minutes, the maximum temperature difference is 0.3 °C
Displacement sensor measurement range: 0-25mm
Displacement resolution: 0.001mm
Displacement measurement accuracy: 0.05mm
Round grinding speed: 21 round trips / min
Wheel surface hardness: 78±2
Wheel rolling load: 0.7MPa±0.05MPa (factory adjustment)
Dimensions: length × width × height
Net weight: 300Kg
Optional:
1.
The number of test wheels is optional, and the maximum support for 4 wheel mills is tested simultaneously (customized).
2.
Wireless Bluetooth Communicator Kit (which allows wireless communication between the laptop and the rut tester within 10 meters of the room)
3.
Test laptop (if Bluetooth communication is selected, you must select a laptop)
[Basic Principles and Structure]
The rutting test of asphalt mixture is to determine the deformation rate of the rut formed by the test wheel moving back and forth under specific temperature and load conditions, which is expressed by the number of walking (ie, dynamic stability) per 1 mm deformation. The rutting tester uses a test piece to fix the test wheel movement method. The test piece was fixed in a constant temperature bath (space), and the test wheel was reciprocated back and forth at a rate of 21 times per minute under the drag of the geared motor and the crankshaft link. As shown in the figure: the test wheel and the load are mounted on the light bar guide and are dragged back and forth. The test wheel crushes the test piece to generate deformation, and the displacement sensor detects a slight deformation. The deformation data and the data of the number of times of the test wheel movement are transmitted to the computer, and after the operation, the deformation curve is displayed.
The load weight (pressure) of the test wheel has been adjusted to 0.7Mpa. The load can be adjusted according to the test requirements. A three-phase motor was adjusted to 21 rpm by the reducer, and the test wheel was dragged 21 times per minute.
[functions and features]
1) Automatic temperature control system with air circulation, internal with constant temperature water tank, can be used for water immersion test. The cabinet temperature control accuracy is up to 0.05 °C.
2) Test wheel air pressure automatic lifting system, eliminating manual operation.
3) The control system is easy to disassemble and the maintenance is simpler.
4) Light touch control interface with backlight, complete LCD display information, test status at a glance.
5) Bluetooth wireless communication, the laptop can be safer away from the console.
6) Automatically test, display the graph, automatically store the data, calculate the dynamic stability, and report the printout.
1. HYCX-1 type rutting sample forming machine Product introduction:
HYCX-1 rut sample forming machine is a new generation product developed by our factory. It is suitable for the production of asphalt mixture test piece by wheel milling in the laboratory. The test piece can be used to determine the high temperature anti-rutting ability of asphalt mixture. It is used to test the mechanical properties of asphalt mixture such as high temperature stability of asphalt mixture ratio design. In line with the People's Republic of China industry standard: JTJ 052 — 2000/T 0703.
Second, HYCX-1 type rutting sample forming machine main features:
This test machine is a highway first-stage laboratory equipment. It integrates mechanical, electrical and hydraulic integration. Compared with similar products, it has the characteristics of small size, high degree of automation, full functions and convenient operation. It is at the leading level in China. With hydraulic control, the pressure of the rolling mill is in the range of 0-20KN, which can be adjusted freely. The height of the test die can be adjusted freely within the range of 30-100MM. The clamping mechanism for installing the test die is advanced, easy to use, safe and reliable. After the test model is installed in the car, it can be automatically centered without any adjustment. The jog cart can be stopped at any position. The number of rolling of the trolley can be set arbitrarily, automatically recorded, and automatically stopped. The temperature of the tile can be set arbitrarily, and the set temperature can be automatically maintained.
With intelligent temperature control instrument, it can set the drum temperature, the number of rolling times and the compaction load. The electro-hydraulic servo system reduces system components and reduces system failure rates. Easy to operate and easy to maintain.
Third, HYCX-1 type rutting sample forming machine main technical parameters:
1. Compaction line load control range: 0-20KN (factory setting: 9KN)
2. Temperature control range: 50 ~ 200 °C (factory setting: 100 °C)
3, temperature control accuracy: ± 5 ° C
4, the number of walking: 6 times / min (12 round trips)
5, power supply: AC three-phase four-wire 380V, 2.5KW
6, the use of the environment:
Ambient temperature: 5 ~ 40 °C
Relative humidity: no more than 75%
7, appearance size and weight:
Dimensions: 125 × 65 × 193 (cm × cm × cm)
Weight: 520kg
Fourth, HYCX-1 type rutting test machine molding machine operation panel description:
Please refer to the operation panel below:
1, the power switch:
Turn the power on by pressing the power switch. Turn the switch to the right to turn off the power.
2. Temperature control operation:
After the main power is turned on, the meter automatically enters the temperature control state and automatically controls the temperature according to the current temperature. When the heater is output, the heating indicator lights up, and the OUT indicator on the temperature control meter is on. When the heating is stopped, the heating indicator and the OUT indicator are off. The system adopts a non-contact solid state relay as an actuator, has no action sound, has small impact on the power grid, and has a long service life.
3. Hydraulic pump operation:
The HYCX-1 rut sample forming machine adopts hydraulic power source. When the hydraulic pump does not start or there is no pressure, the bearing and test model carrier can not start. After the hydraulic pump is started, the pressure at the pumping station starts to rise. After 30 seconds, the pressure can reach the requirement, and the bearing and test model carrier can be operated.
Note: If the hydraulic pump is turned on and the mill cannot be lifted and lowered for 30 seconds, the pump motor may be reversed. Reversing any two lines in the ABC of the power input line.
4, grinding and moving operations:
Press the “Run†button, the mill starts to reciprocate, and automatically stops when it reaches the set number of rolling times. If you need to stop during the run, press the "Stop" button.
If you need to start the mill run again, you need to press the "Reset" button on the "Counter" before you can start the mill again. If the centering operation of the mill is required, set the value of the counter to 1 time to start “runningâ€. When the test model carrier stops, the position is exactly the center of the tile.
5. Basic operation steps of sample forming of HYCX-1 rutting sample forming machine:
step 1. Turn on the main power supply step 2. Set the temperature required for the temperature control table step 3. Set the number of rolling times (N/2)
Step 4. Start the hydraulic station step 5. Place the sample in the test model carrier (after the temperature reaches the set temperature), and step 7. Perform the test mode carrier alignment, reset the counter, set the count value to 1, press the “Run†button step 7. Drop the tile, press the sample step 8. Press "Run", try the test vehicle to start running step 9. When the set number of times (N/2) is reached, the test mode carrier automatically stops running step 10. Step up and down the tile step 11. The test mode is turned 180 degrees, and the repeating steps 3, 5, 6, 7, 8, and 9 are completed. Rise and crush the tile, the sample is finished
Note: N is the number of times required for rolling.
Sixth, HYCX-1 type rutting sample forming machine common faults:
1. The milled tile can't rise, can't fall, and the test model can not move.
Cause: There is no pressure in the pump station. Possible cause: The motor is not running (the sound can be heard), the pump motor is reversed, and the phase sequence of the 3-phase power input line can be changed.
2. The test model carrier can move, and the bearing can not rise and fall.
Cause: Lift valve damage solution: Replace the solenoid valve.
3. The milled tile can be lifted and lowered, and the test model can move the car, but the reason can not be reversed: the travel switch is damaged.
Solution: Replace the travel switch
4. The milled tile can be lifted and lowered, and the test model carrier can't move. The reason is that the moving electromagnetic valve is broken.
Solution: Replace the solenoid valve
5. Counter cannot be counted during rolling process Cause: Counting with proximity switch Damage Solution: Replace proximity switch
6. Temperature control instability Cause: The thermostat parameter is not the best solution: start the parameter self-tuning of the temperature control table.
7. The surface temperature of the tile is lower than the temperature displayed by the temperature control meter.
Reason: Since the temperature measurement point is not on the surface of the tile, the temperature step is a normal phenomenon.
Solution: In the parameter correction of the temperature control table, the temperature is corrected to the actual temperature value of the tile; or, the target temperature of the temperature control table is set higher than the required temperature.
Seven, HYCX-1 type rutting sample forming machine temperature control table setting:
XMTE9000 intelligent temperature controller (temperature control meter) is a universal temperature regulator with built-in fuzzy control algorithm. Combined with traditional PID algorithm, the control is fast and stable. In this machine, the meter uses the PT100 temperature sensor, and the factory has been set to the PID adjustment method. Normally, the parameters of the temperature control table have not been adjusted. If the environment changes, the user can fine tune the parameters according to this manual to achieve the best control effect.
1. Schematic diagram of the instrument panel:
2, set the temperature:
Press the SET button to set the temperature. Press the SET button to flash the data in the lower row of the digital tube, indicating that the meter enters the temperature setting state. Press the ↑ button to increase the setting value, press the ↓ button to decrease the setting value, and then press the SET button. The meter returns to normal operation and the temperature is set.
3. Sensor error correction:
The displayed value can be corrected when it is confirmed that the value displayed by the meter deviates from the actual temperature. Press the SET button for 3 seconds to enter the inner menu of the meter. After selecting the SC or Pb parameters, use the ↑↓ key to correct this parameter. After the correction is completed, press the SET button again to exit (3 seconds). When the instrument is shipped with a correction value of 0, it is necessary to prevent the correct display value from being mistakenly corrected to an incorrect value.
4, PID parameter description:
P: Proportional band setting. When the temperature fluctuates regularly (system oscillation), the proportional band should be increased. When the temperature fluctuates irregularly, the proportional band should be reduced. For systems with large overshoots, the P value should be increased appropriately. Otherwise, the P setting should be reduced.
I: The integral time constant is set. When the temperature fluctuates regularly (system oscillation), the integration time should be increased. When the temperature cannot be eliminated for a long time, the integration time should be reduced. In general, setting I to between 60-240 is suitable for many systems.
D: Differential time setting, the increase of the differential time helps to reduce the over temperature of the system. However, excessive differential time will result in excessive sensitivity to interference. D is generally set to be between 1/3 and 1/5 of I.
T: Control cycle, when the system's temperature rise and fall rate is relatively fast, it should be reduced by T. In general, the smaller the T, the better the temperature control effect of the system. If the master is a relay output, too small T will affect the life of the relay. In general, T is about 20 seconds.
5. About self-tuning:
Whether the PID parameter is appropriate is related to the actual temperature control effect. For ordinary users, manually adjusting the PID parameters is a very tedious task. The instrument has a fast PID parameter self-tuning algorithm, and its parameter setting saves more than 1/3 of the time compared with the general instrument. The tuning method is as follows: The method is as follows: Set the SV to the desired temperature control value, then enter the AT parameter layer, set Sv to 1 and exit, then the ATU indicator flashes, indicating that the auto-tuning state has been entered. Also in the normal state, keep pressing the shift button until the ATU light flashes. The results of the two types of PID auto-tuning are identical. To exit the auto-tuning midway, simply press the shift button in the auto-tuning state. The self-tuning process is a positional control. According to different systems, the temperature will fluctuate greatly during the setting process, and the setting time is also long and short. After the self-tuning is completed, the ATU light stops flashing, and the PID parameters obtained by the tuning are automatically saved. The meter automatically returns to the normal measurement and control state and continues to run with the new PID parameters.
6, setback:
Press the SET button for 3 seconds to enter the inner menu. The parameter Hy is the difference value. The hysteresis control is the upper limit of the set point and the lower limit is the set value minus the difference. For example, the hysteresis is adjusted to 5, when the set value is 100 degrees, when the temperature is heated to 100 degrees, the relay is released, and when the temperature drops to 95 degrees, the relay pulls in. The positional hysteresis control reduces the number of relay actions to extend the life of the relay, but the control accuracy is greatly reduced.
7, parameter list:
Parameter code
Parameter meaning
Description
Setting range
AL1
Upper limit alarm value
Set upper limit alarm
-1999~9999
AL2
Lower limit alarm
Set lower limit alarm
-1999~9999
Pb
Measured value deviation
Sensor correction setting
-100~100
Hy
Hysteresis (switching difference)
Alarm and position control
10-50
P
Proportional band
If it is 0, it is position control
0.0-999.9
I
Integration time constant
If it is 0, cancel the integral function
0-3600
d
Differential time constant
If 0, cancel the differential action
0.0-999.9
T
Control cycle
Relay action cycle
1.0-200.0
At
Turn auto-tuning on/off
0: Off 1: On
0-1
Lock
Parameter lock
0: Do not lock 1: Lock parameter 2 except set value: Lock all parameters
0-2
Press the SET button for 3 seconds to enter the user's working parameter setting state. Press the SET button again for 3 seconds to exit the parameter setting.
Eight, HYCX-1 rut sample forming machine set pressure load operation:
1. Schematic diagram of hydraulic pump station:
2. Fill the hydraulic oil:
The pump station must be filled with hydraulic oil before use. If the oil is insufficient, the pressure will not reach the set value, and even the bearing and the sample carrier will not work. Referring to the illustration, open the oil filling port, put the funnel into the funnel, and add 15 liters of hydraulic oil. After filling, tighten the fuel tank cap.
3, pressure roller pressure adjustment:
For the piston cross-sectional area of ​​the hydraulic cylinder configured in the HYCX-1 rutting sample forming machine, the corresponding relationship between the pressure and the pressure is 1 MPa, and the corresponding pressure is 9.8665 KN. Due to the limited display accuracy of the pressure indicating instrument, pressure adjustment or calibration requires a standard pressure gauge for auxiliary debugging.
Proceed as follows:
1 Press the hydraulic pump switch to start the pump station and open the front chassis guard to expose the regulating valve of the hydraulic station.
2 Place the pressure sensor directly under the tile, the range should not be less than 20KN.
3 After starting the hydraulic station for 10 minutes, open the bearing down switch to make the bearing vertical pressure on the pressure sensor.
4 Adjust the total pressure regulating valve, observe the pump station pressure indicator, and adjust the total pressure to 1MPa~1.2MPa. The total pressure depends on the desired final pressure value. If the required pressure on the mill is 1 MPa, the total pressure should not be lower than 1 MPa and adjusted to slightly above the required pressure.
5 Adjust the pressure regulating valve of the bearing, observe the value of the pressure gauge, and adjust to the required value. The factory has been adjusted to 9KN.
6 After the adjustment is completed, tighten the tightening nut of the pressure regulating valve with a wrench.
4. Sample carrier speed adjustment:
1 Press the hydraulic pump switch to start the pump station and open the front chassis guard to expose the regulating valve of the hydraulic station.
2 Start the hydraulic station, place a wooden board with a thickness of not less than 40mm or other items that can withstand 1 ton of pressure on the specimen carrying vehicle, open the rolling down switch, and press the bearing to the block.
3 Press the “Run†button to start the load carrier, adjust the speed control valve of the sample carrier, test the running speed of the sample carrier, and slowly adjust to the required speed. The speed regulating valve has an adjusting button before and after, respectively, to adjust the moving speed of the carrying vehicle back and forth.
German type cable reel Non-rewirable, 230V~, IP20, Class I, with a thermal cut-out, with a non-rewirable plug with cord H05VV-F 3G1,0-1,5mm 2 ,
with 4-way socket outlet with or without shutters.
Germany Cable Reel,Cable Reel,Automatic Cable Reel,Cable Spool Reel
CIXI KYFEN ELECTRONICS CO.,LTD, , https://www.kyfengroup.com