The field of new energy vehicle power lithium battery recycling mainly targets the fields of ICT, home and renewable energy generation and energy storage. Although the practice of power lithium battery recycling has not been carried out in China, it has had many years of demonstration experience in Japan and the United States. Japan and South Korea have been focusing on the research of power battery recycling since the beginning of the development of new energy vehicles. These preliminary research work has provided a good reference for China to carry out battery recycling research.
This article refers to the address: http://
Now the domestic automobile power recycling industry has just started. In 2015, the total number of scrapped power batteries was 20,000 to 40,000 tons, and the corresponding battery recovery rate was only 2%. The current recycling capacity is simply unable to afford the 120,000 to 170,000 tons of scrapped batteries expected in 2020. Therefore, many problems in the construction of recycling management system, advanced technology innovation, model exploration, and standard system construction need to be solved urgently.
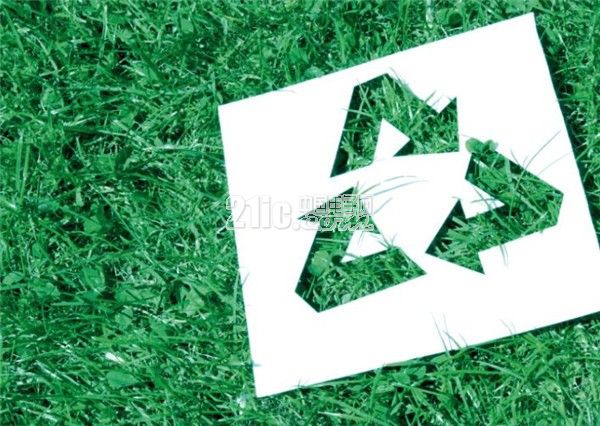
First, the main problems of the automotive power battery recycling industry
1) Dismantling process of used car power battery is complicated and has safety risks
Since the domestic power battery has no uniform and compliant regulations in terms of size and structure specifications, now the domestic battery manufacturers belong to the Eight Immortals, and the seas are all brilliant. The battery system design is completely different, making it impossible to use the same set of disassembly pipelines for all battery packs and modules, resulting in extremely inconvenient battery disassembly. If automated dismantling is required, the battery packs and modules of different sizes and shapes will require high flexibility in the production line, resulting in high disposal costs. At present, the domestic people basically rely on manual dismantling. The skill level of workers directly affects the efficiency of the battery recycling process. At the same time, due to the high energy of the battery pack itself, various safety problems such as short circuit and liquid leakage may occur, which may cause fire or explosion. , resulting in casualties and property damage. Therefore, companies need to carefully study the safety and efficiency of the battery pack disassembly process.
2) Poor product consistency and remaining life and battery status cannot be systematically evaluated
Waste vehicle power batteries must pass quality inspection when re-using the ladder, sorting the batteries, including safety assessment, cycle life test, etc., sorting the cells, and then re-using them. However, if the power battery does not have a complete data record during service, the accuracy of the battery life prediction may be reduced, the battery consistency may not be guaranteed, and the cost of test equipment, test cost, test time, analysis modeling, etc. Will increase. Due to the same internal resistance, electrochemical and thermal properties of different batteries, battery inconsistency and reliability may not be guaranteed. If some of the problematic batteries are not tested during the screening process, they will be used again. The safety risks of other entire battery systems. Therefore, how to achieve fast and non-destructive and accurate detection is the key to the use of cascades in this case.
Recently, the state issued GB/T 32690 "Electric Vehicle Remote Service Management System Technical Plan", which includes the collection and monitoring of new energy vehicle operation data as a mandatory requirement for enterprises, and will make up for this data gap in the future after implementation. .
3) System integration technology is not mature
Since the connection between the cells is usually laser welding or other rigid connection process, it is difficult to achieve non-destructive disassembly. The most reasonable use of the power battery cascade is to disassemble to the module level, but different batches or even different manufacturers produce Battery modules, to be mixed in the same system, need to consider and solve the following system integration technology: grouping technology: re-group battery modules and establish databases according to parameters such as material system, capacity, internal resistance, and residual cycle life. The grouping parameter setting should be reasonable. If the parameter setting interval is too large, the module discreteness is large. After the group is the system, the system performance and life are greatly affected. If the parameter setting interval is too small, the grouping is too strict, which may result in There are fewer matching modules and system integration is difficult. Flexible design of the system: When designing the system structure, it is necessary to fully consider the size, weight and number of series and parallel connections that different modules may have. Therefore, the design should be flexible in space to be compatible with different modules. Considering the tightness and reliability, it is also necessary to consider the elasticity and facilitate quick loading and unloading.
4) Recycling economy is not good
The vehicle power battery must be pretreated before it is recycled, including discharge, disassembly, crushing, and sorting. The plastic and metal casing after disassembly can be recycled, but it is costly: because the residual voltage is still up to hundreds of volts (excluding the 18 6 50 battery), there is a certain danger; the battery casing is not self-removable for safety reasons. The form of opening up takes a lot of effort. As far as the pre-processing is concerned, it is definitely a loss-making business.
Even lithium batteries, cathode materials are also diverse, the mainstream are lithium cobaltate, lithium manganate, lithium nickel cobalt manganese oxide, lithium iron phosphate and so on. The metal oxide is extracted by leaching with an acid-base solution and then subjected to various chemical procedures. However, the composition of these oxides is different, and the mixture is more difficult. The battery is classified according to the positive electrode material in advance, and the cost is not low. Recycling the positive metal is already the most profitable part of the battery recycling line. But the process is too complicated, and the companies that settle the accounts are discouraged unless the metal price is as high as in 2011. Now that the prices of bulk commodities and non-ferrous metals and rare earth products are at a low level, it is not cost-effective to recycle metals by these methods, let alone troublesome waste disposal afterwards. According to the current state of the art, a single waste liquid treatment is enough to eat the poor recovery metal revenue. The negative electrode material is graphite (the silicon battery is only the size of the laboratory), the material is too cheap and can only be disposed of by landfill. Fortunately, graphite itself does not pollute the environment and only takes up space. Under the current technical conditions, no company will actively invest in the recycling industry.
Summary : There are many kinds of domestic power batteries, the battery structure is complex and there is no fixed standard, resulting in complicated dismantling and recycling process, high recycling cost, lack of recycling enthusiasm, difficulty in industrialization, and lack of restructuring techniques. Policy, power battery recycling is facing great difficulties.
Second, the development direction and trend of recycling industry
1. The management system needs to be further clarified, and the rewards and punishments need to be clearly defined
In order to strengthen the management of the comprehensive utilization of waste energy and power storage batteries for new energy vehicles and standardize the industry and market order, the Ministry of Industry and Information Technology has successively formulated the "Standard Conditions for the Comprehensive Utilization of Waste Energy Storage Battery for New Energy Vehicles" and its supporting "New Energy Vehicle Waste Power Battery" Interim Measures for the Comprehensive Management of Industry Regulations Announcement.
Since the beginning of this year, the government departments have focused on the research and development of the “Management Measures for the Recovery and Utilization of Power Battery for New Energy Vehiclesâ€. The formulation of the “Measures†is based on the concept of the Extended Producer Responsibility System and is based on the management of the life cycle of power battery products. The "Measures" cover the relevant stages of product design, production, sales, recycling, cascade utilization, recycling, etc., and clarify the power battery production enterprises, automobile production enterprises, cascade utilization enterprises, and scrap car recycling and dismantling enterprises to undertake the recycling of power batteries at various stages. Related responsibilities. Visually, this is also to prepare for the compulsory supervision in the future. Under the premise of the basic national policy of environmental protection, no company dares to touch the high-voltage line. Even if it only copes with the supervision, it will pile up the used batteries in the warehouse and avoid large-scale unsupervised conditions. Secondary pollution.
2. Urgent need to establish a power battery recycling standard system
At present, China's key technologies for the evaluation of residual value and health status of decommissioned power storage batteries are still immature. The research and development of related technologies for cascade utilization and recycling are relatively lagging. It is necessary for industry experts to cooperate and promote technological innovation and application. Technical Difficulties. For example, in the case of battery disassembly, flexible configuration is required, and the disassembly pipeline is segmented and refined. For different battery packs, when constructing the disassembly operation process, it is necessary to reuse the existing assembly line and process as much as possible. To improve work efficiency and reduce duplication of investment. At the same time, it is necessary to completely record the running data of the power battery during the service period, and the manufacturer of the ladder can establish the life model of the battery module based on the data.
The current battery battery recycling urgently needs technical standards, the battery capacity needs to enter the recycling process, to what extent can be used in the next step, and to what extent can not be used again, there is no clear standard can be referenced, which requires the establishment of relevant specifications at the government level And standards. At a deeper level, if the external dimensions and internal structure of the power module are used as a relatively uniform regulation, it will save huge expenditures for the downstream battery recycling industry, and will further reduce the battery cost of the ladder. The solution has created possibilities and is of great help to the advancement of the battery recycling industry. According to the gossip, the current regulations in this area are in the pipeline, and I wonder if it will be released and implemented soon.
3. Establish a new business operation model and find profit points
For power battery recycling, we only have to research technology to improve metal smelting efficiency and reduce costs. If we have scale effect, we can stand firm under the national subsidy and support policies, and then we can still have a lot to do.
For the use of derivative products for the power battery ladder, the customer will have doubts about the performance, life, reliability and safety of the product under the informed circumstances, and the promotion of the product will have certain obstacles. In the promotion and application of products, we must fully consider the status quo and appeals of customers, and combine various business operation methods to obtain their own interests on the basis of fully helping customers to make profits. You can learn from some of the successful experiences of other industries, such as installment payment, time-sharing, post-profit settlement, custody operations, and even free supply (subsequent value-added services), to explore effective business models for the use of ladders.
Summary: At present, the operating mode of the domestic automotive power battery recycling industry is still in the groping stage. Now the government is urgently involved, and the company is gradually embarking on a healthy development path in formulating policies and establishing standards. It is also necessary to set up industrial alliances in the upstream and downstream industries to establish a healthy industrial chain and find viable profit points.
Third, learn from the experience of Japan
Until today, Japan has no specific regulations for power batteries. However, under the circumstances that Japan's environmental protection laws (the "Efficient Use of Resources", "Energy Conservation Law" and "Renewable Resources Law") are clear, there is no reason to separately formulate a law for power batteries, and the law itself cannot solve technical problems.
Japanese companies started in the field of new energy vehicles more than ten years earlier than us. Toyota's Prius was born in 1997. According to Japanese people's great emphasis on garbage collection (national waste disposal rate reaches 100%), Japan should establish a power battery recycling industry chain within five years of the birth of a new energy vehicle, but it does not. Even for Toyota, the recovery of nickel-metal hydride batteries (power batteries for hybrid vehicles) is also facing an unprofitable dilemma.
Japan did not start the recycling of nickel-hydrogen battery projects in Japan until 2011. At home, Toyota and Sumitomo Metal cooperated, with the world's first-class high-purity extraction technology, Toyota realized the multiple use of nickel in the hybrid vehicle power battery, which can recover 50% of the nickel in the battery pack; Chemical Engineering and Sumitomo Metal Mine are equipped with a dedicated production line that can recycle the equivalent of 10,000 hybrid car batteries per year; in 2012, Honda worked with Japan's Heavy Chemical Industry Co., Ltd. to do similar things. However, the Honda recycling program can recycle more than 80% of rare earth metals for the manufacture of new nickel-metal hydride batteries. A few years ago, nickel recovered from hybrid car batteries could only be used to produce stainless steel. With the development of high-precision nickel extraction and separation technology, the recovered nickel can now be used to produce new batteries. Toyota has promoted nickel recycling technology to overseas plants.
Although recycling batteries is the responsibility, Japanese companies rely on recycled metals (including rare earth elements that are extremely valuable to Japan) as a driving force for the recycling industry.
In Europe, Toyota has shown a more positive attitude, which is related to more stringent environmental regulations in Europe. Toyota announced last year that it has achieved a 100% recycling target for hybrid vehicles, with a previous recovery rate of 91%. Toyota also extended the partnership between SNAM (France) and Umicore Group (Belgium), which will recycle nickel-metal hydride batteries and lithium batteries. Toyota (including Lexus) has sold a total of 85,000 hybrid cars in Europe since 2000, which is larger than the current number of new energy vehicles in China. At the same time, in order to extend the life of the power battery, avoid processing peak capacity limits. Toyota also promoted the power battery ladder utilization project. Last year, Toyota used the used batteries of the Camry Hybrid for the energy storage of the Yellowstone National Park facility. Nissan also cooperated with Sumitomo to develop a battery system using a waste lithium battery that is powered by electric vehicles, as an auxiliary energy storage system for solar power generation, for independent power supply at night and under-light conditions. 4REnergy, a joint venture between Sumitomo Corporation and Nissan, aims to commercialize the use of EV waste lithium batteries for electric vehicles. Since its establishment five years ago, the company has become the most successful lithium battery recycling company in business.
KNL1-63 Residual Current Circuit Breaker
KNL1-63 Moulded Case Circuit Breaker is MCCB , How to select good Molded Case Circuit Breaker suppliers? Korlen electric is your first choice. All moulded Case Circuit Breakers pass the CE.CB.SEMKO.SIRIM etc. Certificates.
Moulded Case Circuit Breaker /MCCB can be used to distribute electric power and protect power equipment against overload and short-current, and can change the circuit and start motor infrequently. The application of Moulded Case Circuit Breaker /MCCB is industrial.
Korlen electric also provide Miniature Circuit Breaker /MCB. Residual Current Circuit Breaker /RCCB. RCBO. Led light and so on .
KNL1-63 Molded Case Circuit Breaker,KNL1-63 China Size Molded Case Circuit Breaker,KNL1-63 Electrical Molded Case Circuit Breaker,KNL1-63 Automatic Molded Case Circuit Breaker
Wenzhou Korlen Electric Appliances Co., Ltd. , https://www.korlen-electric.com